tedrive
Headquartered in Germany, tedrive Steering is a specialised development partner and manufacturer of steering systems for the global vehicle market. The product portfolio encompasses rack-and-pinion, as well as recirculating ball steering gear systems across all vehicle segments, from small passenger cars to large trucks and buses.
During the ResCoM project, tedrive continued its existing investigation of remanufacturing steering systems, specifically for its hydraulic rack and pinion steering gears for passenger cars and light commercial vehicles. Remanufacturing activities allow greater value to be captured from materials by collecting used products and bringing them back to an ‘as new’ condition. tedrive's aims for ResCoM were to understand the business case for the expansion of its remanufacturing activities and the challenges associated with using its products longer. Given that steering gear is a safety item, there were special requirements which needed to be considered in the concept.
Outcomes of the ResCoM Pilot
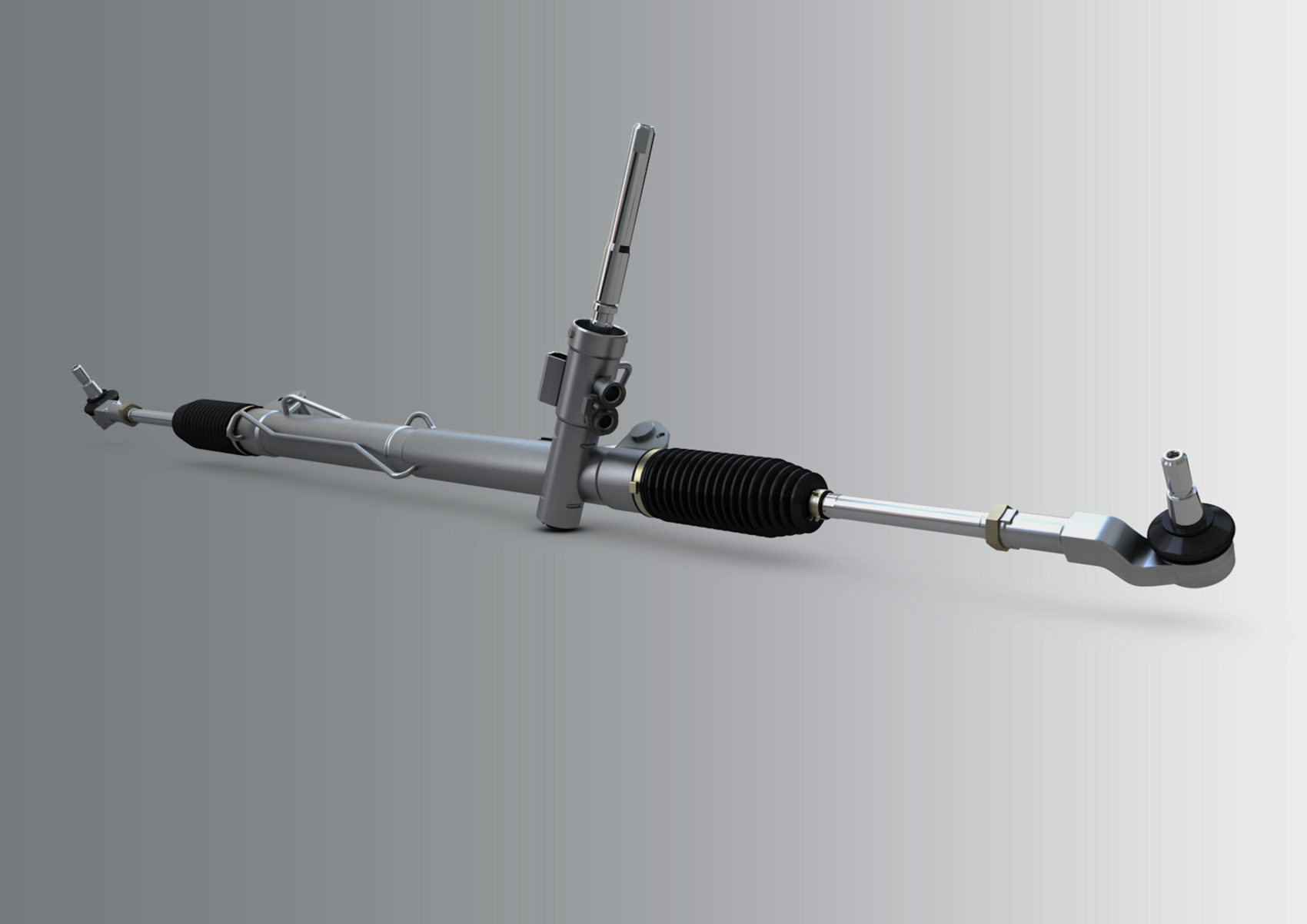
By participating in the ResCoM project, tedrive was able to gain a number of insights with regard to the challenges of expanding its remanufacturing operations. Using the Reman Design Checklist, tedrive was able to assess the future ability to remanufacture products during the design phase, which highlighted how a design change at the component level could facilitate easier remanufacturing of an entire product.
tedrive used the ResCoM Analytical Tool, Multimethod Simulation and MI:BoM Analyzer, to investigate and compare the economic and environmental performance of three different potential scenarios for remanufacturing, in comparison to the linear model used in the automotive industry today. Although some of the scenarios showed positive economic and environmental performance, a key challenge was getting products back at an attractive price. Acquiring used steering systems can be expensive, and therefore a reasonable volume, and efficient reverse supply chain is needed to build the business case. It was recognised that better collaboration with car manufacturers to collect tedrive’s own steering systems could support a viable business case by facilitating easier return of the used products. Additionally, poor transport conditions meant that some returned products could not ultimately be remanufactured once they arrived with tedrive.
The acquisition of used products was further challenged, as legislative barriers preventing the use of remanufactured components in new vehicles reduced the potential market for the products. From the analyses of the tedrive case, it became clear that under current conditions there would need to be a significant reduction of costs for acquiring the used parts, or a greater scale of operations needed to be achieved. For example, allowing the use of remanufactured steering gears for the production of new vehicles, which would increase demand for the remanufactured parts.
Going forwards
tedrive will continue seeking to increase the efficiency of its reverse supply chain and further investigate options for increased collaboration with car manufacturers. Design improvements for investigation include - updating the design for easier remanufacturing of the steering system, and investigating the packaging design to reduce damage of steering systems during transportation.