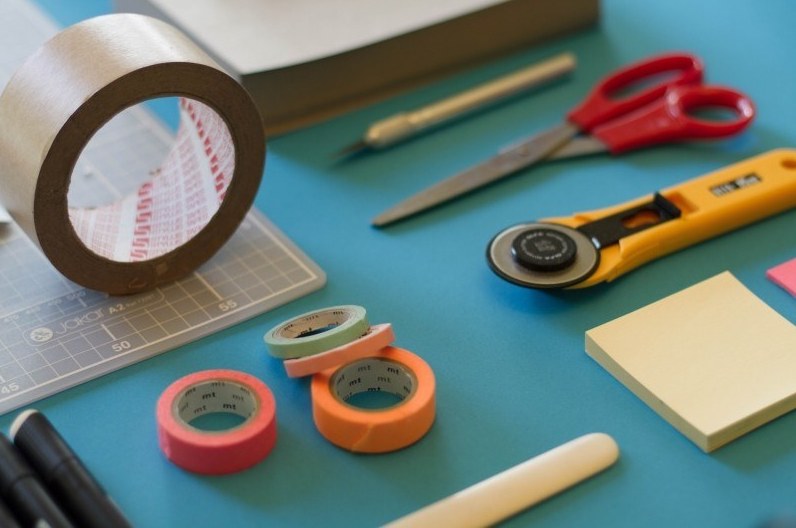
The four year ResCoM project which officially concludes at the end of October, has seen 12 consortium partners from academia and industry, supporting manufacturers to adopt a systemic approach to applying circular economy principles in their product designs.
The Resource Conservative Manufacturing (ResCoM) project started in Autumn 2013, to help manufacturers ‘close the loop’ and capture value through rethinking the relationships between materials, product design, supply chains, business models, and technology.
Co-funded by the European Union, ResCoM has developed and tested an innovative methodology and software platform for the industrial implementation of closed-loop manufacturing systems. This helps designers and manufacturers understand how collection, remanufacturing, and reuse of products can lead to more profitable, resource-efficient, and resilient business practices, compared to the current predominantly linear manufacturing system.
Today, the ResCoM consortium makes the new platform, methodology, and supporting case studies, publicly available.
The methodology and tools support manufacturers in transitioning to closed-loop products that are designed for multiple life cycles. The tools help guide company decisions by illustrating the benefit of products designed in this way, highlighting economic impact, resource efficiency, greenhouse gas emissions, and energy use.
“In 2013, ResCoM set out an ambition to support manufacturing companies in their transition from linear to circular business strategy. The new tools, methods and software platform developed in the project will now play a vital role in providing support towards this ambition – from circular product ideation to multiple lifecycle management.” Amir Rashid, Associate Professor & Head of the MMS division at the Department of Production Engineering - KTH Royal Institute of Technology.
Four industrial pilots have been conducted through ResCoM to test and develop tools. The evidence gathered strongly suggests that circular business models should be employed in the early stages of a company's product development process, and manufacturers can use the ResCoM methodology and tools to make this happen in practice.
“The ResCoM tools and methodologies have successfully supported Gorenje to identify opportunities to capture value from circular business models. Having developed a service-based concept for our ASKO washing machine throughout ResCoM, we have now moved beyond theory and into implementation with an application of a large-scale industrial pilot of this model with EU Horizon 2020 funding. We are looking forward to new challenges.” Janez Uplaznik, Executive Vice President for Joint R&D.
Click to explore the tools, platform, and case studies, now available. The project officially concludes on 31st October 2017.